
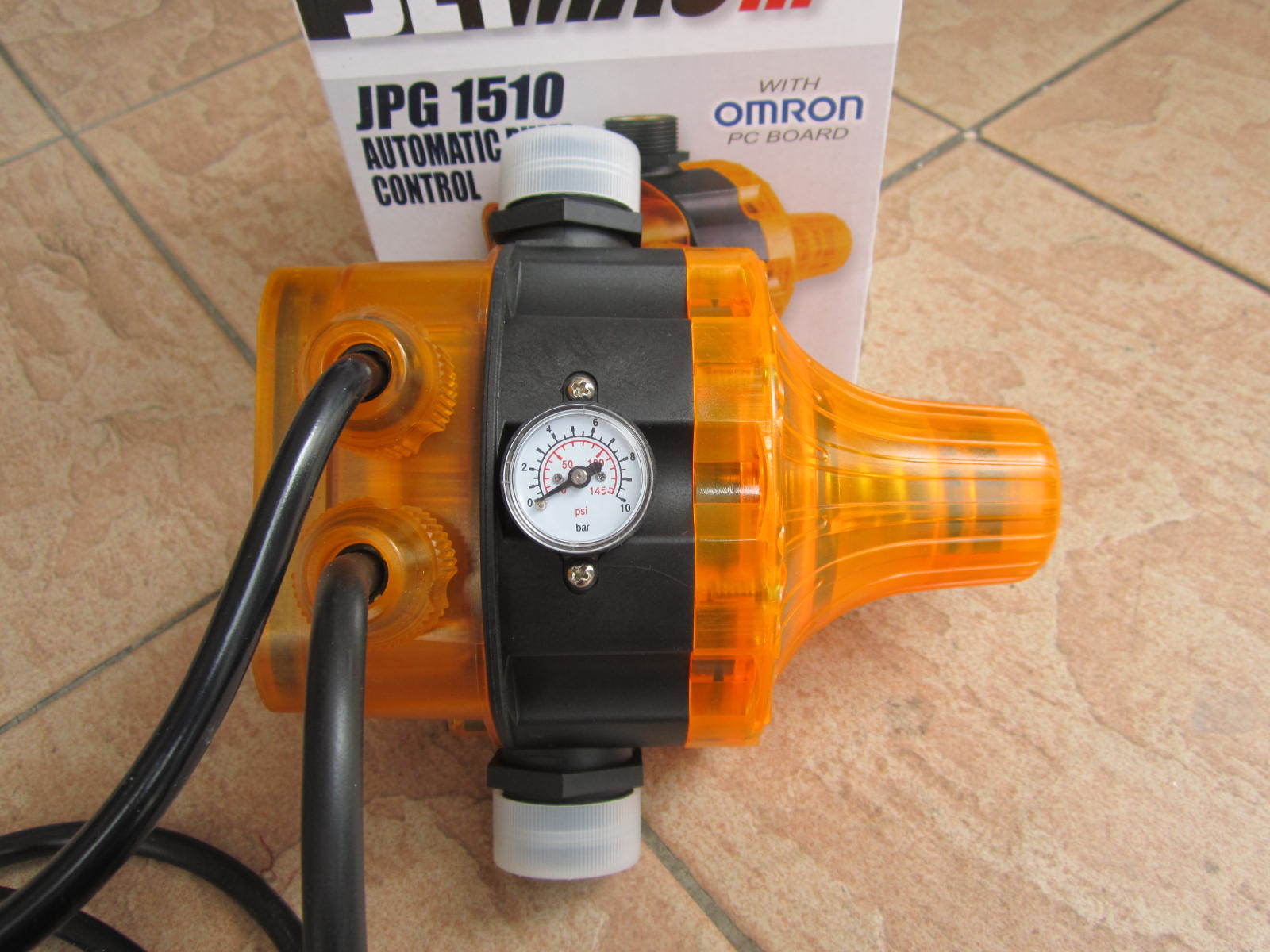
Several hardware options also are available to control the multiple injection pumps involved in a multi-zone minitube system. Low pressure drop in the headers and hydraulic separator creates very little tendency for the circulators to interact with each other. This will result in very little pressure drop along the length of the headers. My suggestion is to select a piping size that keeps the maximum flow velocity at around 2 ft. It is important to generously size the headers on both sides of the hydraulic separator. Hydraulic separation between the injection pumps and boiler circulators.Īrguably, these functions could be provided using other multiple hardware components, but not with the installation simplicity and minimal space requirement offered by the “3-in-1” functionality of the hydraulic separator. This device provides three desirable functions: This system uses a hydraulic separator between the boilers and injection pumps. If the mixing were done in the mechanical room, the required flow rate to and from this manifold station would be (See Formula 3):įigure 3 shows the modern way to set up a multi-zone minitube system.
#MINITUBE CONTROLLER FOR AUTOMATED DISP PUMP PLUS#
of supply plus return piping required between the mechanical room and this manifold station. Also assume the piping between the mechanical room and manifold station is routed vertically upward to a 25-ft.-high ceiling and then back down to the manifold station. away from the mechanical room in a large highway garage. To see why this is an advantage, consider a situation in which the manifold station supplying 250,000 Btu/hr. The minitube approach takes advantage of these small piping sizes and “stretches them out” from the mechanical room to the manifold station as shown in Figure 2. This relatively low flow rate can easily be handled by 3/4-in. Determine the required injection flow rate (See Formula 2). Hot water from a cast-iron boiler is available at 180° F. The supply water temperature to the floor circuits under those conditions is 110° F and the water returns from the circuits at 90° F. to a heated floor slab in a large garage under design load conditions. K = A constant depending on fluid used (For water, k=490 For 30% glycol solution, k=479 For 50% glycol solution, k=450).įor example, assume a large manifold station is supplying 250,000 Btu/hr.

∆T = Temperature difference between supply and return injection risers (☏). Q = Rate of heat transfer to distribution system at design load (Btu/hr.). This relationship is given by Formula 1.įi = Required injection flow rate at design load (gpm). The greater this temperature difference is, the lower the required injection flow rate. The required injection flow rate for any injection mixing system is inversely proportional to the temperature difference between the hot water being injected and the cooler water returning from the manifold station. In many cases, this temperature difference is four or more times greater than the temperature drop across the manifold station. the boiler outlet temperature minus the floor circuit return temperature). The piping between the mechanical room and manifold station is now sized for the flow rates associated with a much higher temperature difference (e.g. In minitube systems, the mixing takes place at the manifold station(s). Using this approach, the piping between the mechanical room and manifold station(s) must be sized for the flow rate associated with a typical manifold temperature drop of 15° F to 20° F. The piping details for a typical injection mixing system are shown in Figure 1. Most injection mixing systems used with radiant floor heating perform the mixing in the mechanical room and distribute relative low temperature water to manifold stations. Reduced flow rates allow for smaller piping and smaller circulators. This high temperature difference allows a relatively low flow rate to carry a significant amount of heat. Like most injection mixing applications, minitube distribution systems leverage the high temperature difference between a “hot” boiler and a low temperature heating distribution system. They are well-suited to projects where a conventional boiler that operates with water temperatures in the range of 160° F to 180° F under design load conditions supplies a low temperature load such as slab-type floor heating. Minitube distribution systems are a specialized application of injection mixing. This is where a minitube distribution system might save several thousand dollars.
